Table of contents
- What is PDCA?
- How does the PDCA cycle work?
- How to use the PDCA cycle for lasting results
- The key benefits of using the PDCA cycle
- When to use the PDCA cycle…and when to try something else
- Common challenges with PDCA and how to overcome them
- Create a plan for continuous improvement, with Dropbox as your base
So you’ve got a problem on your hands: It’s thorny, complex, and layered. The PDCA Cycle can be your secret weapon.
What is PDCA?
Similar to the Japanese concept of Kaizen, PDCA is a simple, step-by-step approach to tackling challenges and streamlining processes.
This iterative method is all about testing solutions, analyzing results, and continuously improving. Businesses and organizations can use it to systematically analyze and improve their processes for efficiency, quality, and overall performance.
What does PDCA stand for?
PDCA stands for Plan, Do, Check, Act. Coined by W. Edwards Deming (known as the "father of modern quality control"). This strategy involves four phases—Plan, Do, Check, Act—each crucial to fostering sustainable organizational growth:
- Plan: Define goals and what needs to change
- Do: Implement the changes on a small scale
- Check: Analyze the results to see if the changes worked
- Act: Standardize successful changes or try again with a new plan

This cyclical approach allows organizations to continuously refine processes for better efficiency, quality, and performance.
What kinds of organizations use the PDCA Cycle?
An extremely versatile system, PDCA is used by many types of businesses because it provides a structured approach to test ideas, gather data, and make data-driven decisions for ongoing improvement. For example:
- Manufacturing: A manufacturing company can use PDCA to enhance product quality.
- Customer service: A department can implement PDCA to give better service.
- Software development: Developers can use it to build better software.
- Healthcare: A hospital can apply PDCA to improve patient care standards.
How does the PDCA cycle work?
A PDCA cycle involves four steps: Plan, Do, Check, Act. It can be used to solve specific problems, make changes to processes or systems, or track and measure progress.
Plan
- Set goals: Define specific, measurable, achievable, relevant, and time-bound (SMART) goals.
- Identify resources: Determine the resources needed to achieve your goals.
- Develop a plan: Outline how to accomplish your goals and measure progress in a shareable, collaborative document.
- Understand current states: Assess your organization’s current state and the desired state.
- Customize approach: Tailor the PDCA cycle to fit your needs, possibly incorporating additional steps like the DMAIC process.
- Focus on data: Use pre-existing data or insights from previous PDCA cycles to inform your approach
Do
- Implement the plan: Take action on your plan, treating it as an experiment.
- Test changes: Conduct small-scale tests in a controlled setting to avoid disrupting other processes.
- Collect data: Gather information during this phase to inform the next steps—you can use Dropbox cloud storage to securely store and easily access your data files.
Check
- Analyze results: Review the data collected during the Do phase to see if you’re meeting your goals.
- Compare to goals: Evaluate the outcomes against the original goals.
- Assess the approach: Determine if changes to the plan are needed, and repeat the Do and Check phases until a satisfactory solution is found. Sharing your findings with others to get their feedback will help ensure your findings are robust.
Act
- Implement changes: Apply the successful changes identified in the Check phase.
- Continuous improvement: Use the results as the new baseline and continue the PDCA cycle to foster ongoing improvement. Try to centralize this in one document to keep track of what worked each cycle.
How to use the PDCA cycle for lasting results
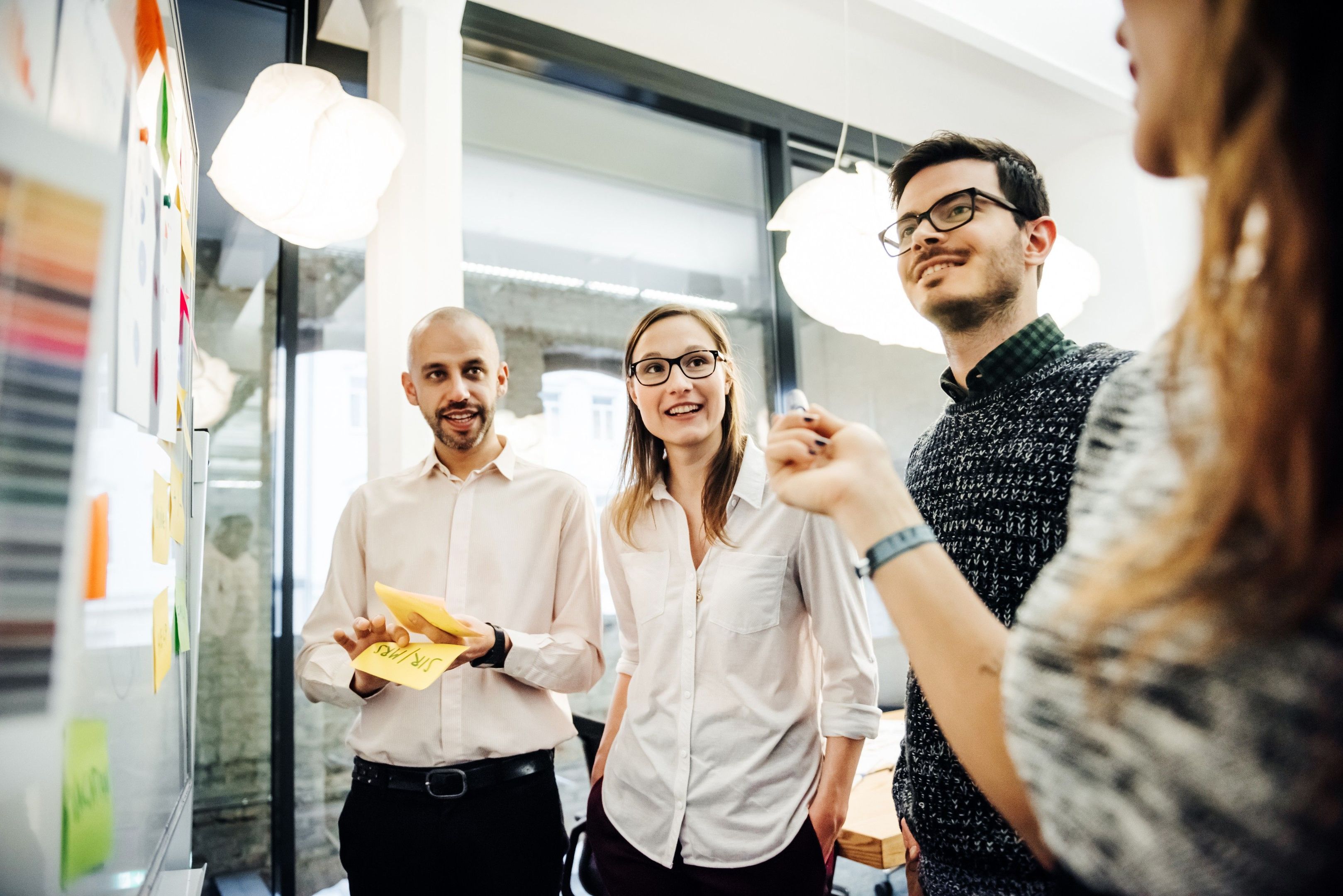
The PDCA cycle is continuous, allowing for repeated iterations to refine and enhance processes and products. To successfully implement the PDCA cycle and achieve lasting results, you just need to keep a few key elements in mind throughout the process.
1. Set clear goals
Establish specific, measurable, achievable, relevant, and time-bound (SMART) goals. Clear goals provide direction and focus for improvement efforts and help evaluate the effectiveness of the PDCA cycle.
2. Involve key stakeholders
Engage stakeholders at all levels of the organization to ensure diverse perspectives and broad support. This fosters ownership and commitment to the process.
3. Allocate resources and set timelines
Ensure adequate personnel, financial resources, and technology are available. Set realistic timelines to maintain momentum and prevent burnout.
4. Monitor progress and analyze results
Regularly track progress using key performance indicators (KPIs). Use tools to track document engagement and analyze the data to gauge performance and find areas for improvement.
5. Promote a culture of continuous improvement
Encourage feedback and proactive issue resolution. Provide continuous learning opportunities to enhance employee skills and knowledge, enabling effective contributions to the improvement process.
The key benefits of using the PDCA cycle
The PDCA cycle encourages structured problem-solving, fosters a culture of continuous learning, enables data-driven decision-making, and drives adaptability within processes.
Structured problem-solving
The PDCA cycle provides a systematic approach to identifying issues, implementing solutions, and measuring progress. This structured framework promotes a disciplined method for problem-solving and improvement efforts.
Culture of continuous learning
PDCA fosters collaboration, not silos. By involving employees in all stages, it creates a shared understanding of goals and processes. When employees participate in identifying problems, developing solutions, and monitoring progress, they gain a deeper understanding of work processes and organizational goals. This collaborative environment sparks innovation, with team members sharing insights and building a culture of continuous learning.
Data-driven decision-making
The PDCA cycle ensures improvements are based on concrete evidence rather than assumptions. By collecting and analyzing data at each stage, organizations can make informed decisions about the effectiveness of their efforts, minimizing the risk of implementing ineffective solutions.
Adaptability and responsiveness
The PDCA cycle promotes regular progress reviews and adjustments, enabling organizations to respond swiftly to new challenges or opportunities. This flexibility helps organizations stay competitive in dynamic environments, continuously improve processes and products, and maintain a competitive edge.
When to use the PDCA cycle…and when to try something else
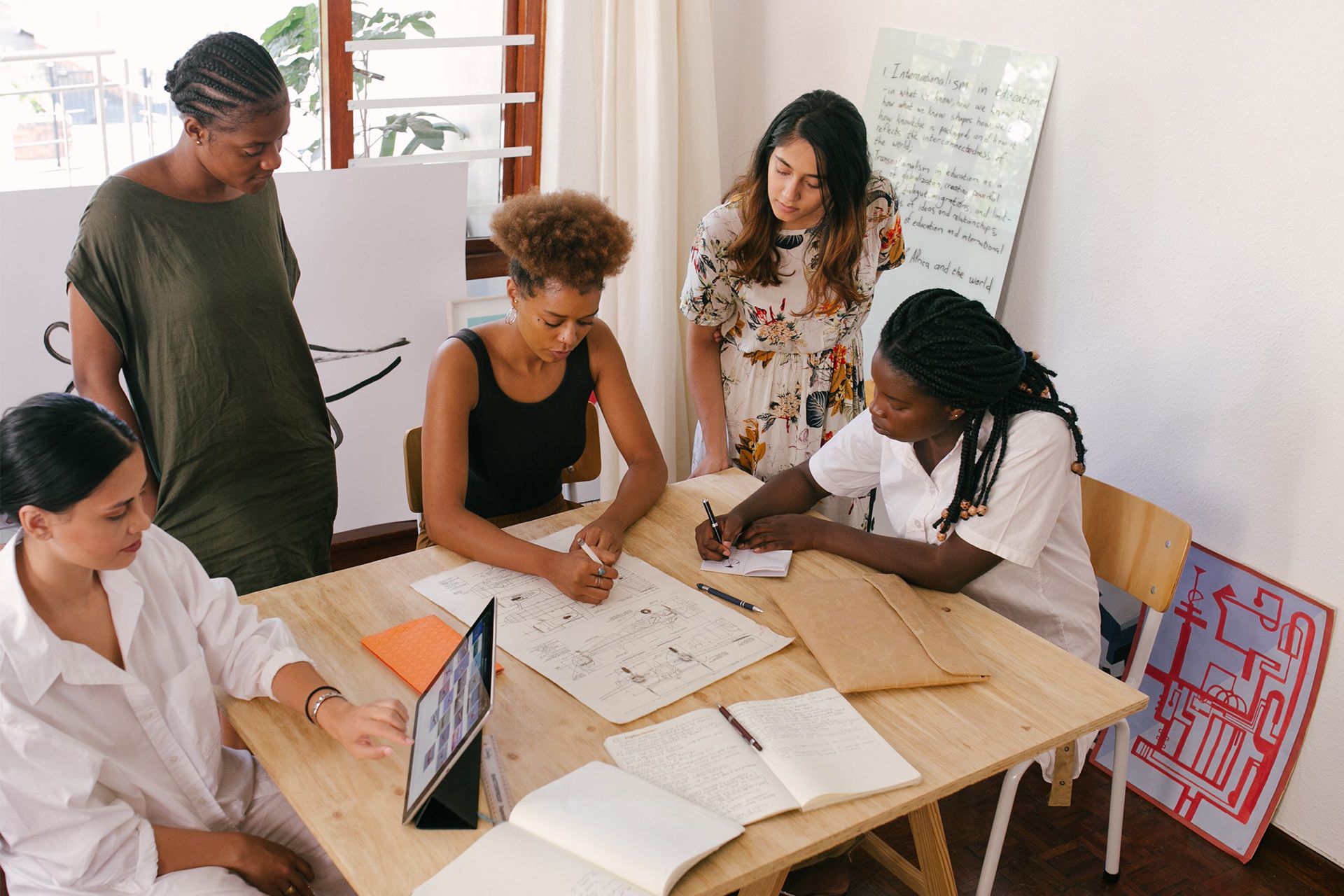
Some problem-solving and management approaches can be time and resource-intensive to apply. However, PDCA’s flexibility lends itself to solving many issues on the cheap. That said, PDCA isn’t suitable for every issue your organization encounters.
When you should use PDCA
If you are looking to make consistent improvement to work processes, PDCA is a good bet.
The cycle’s strength is in its ability to continually identify problems, then refine and find optimal methods. It’s less likely to completely transform performance metrics, for example, after a singular iteration.
Its simplicity belies PDCA’s strength: It requires rigor and mastery in order to truly benefit from it. But by adopting it—and sticking with it—you have a measurable way to create change in the way you or your team work. Successfully employing it at an organization can help move all your colleagues toward a mindset of problem-solving and critical thinking. What’s better than that?
When you shouldn’t use the PDCA cycle
If you’re someone who needs to see instant results, though, PDCA may not be for you. So if your organization is dealing with an urgent process-oriented issue or you need fast turnarounds in performance and results, PDCA may not be the right fit.
Common challenges with PDCA and how to overcome them
Despite its effectiveness, implementing the PDCA cycle can present various challenges. Acknowledging and addressing these obstacles is crucial for successful implementation. Here are some common challenges and strategies to overcome them:
Resistance to change
Employees may resist changes introduced by the PDCA cycle, fearing disruptions to their routines. To overcome this, involve them in the planning phase, actively listen to their concerns, and emphasize the benefits of continuous improvement.
Lack of resources
Resource constraints, such as time, budget, and expertise, can hinder the effective implementation of the PDCA cycle. Prioritize improvement initiatives, allocate resources wisely, and seek support from senior management to secure the necessary resources.
Data collection and analysis
Gathering and analyzing data can be time-consuming and complex. Leverage technology and data analytics tools to streamline data collection and analysis, making the process more efficient and accurate.
Lack of accountability
Without clear accountability, the PDCA cycle may falter. Assign specific responsibilities to individuals and teams, ensuring that each step of the cycle is diligently executed. Regular progress updates and performance reviews can reinforce accountability.
Sustaining the improvement process
Continuous improvement requires ongoing commitment and effort. Establish a culture that values learning, adaptation, and innovation. Celebrate successes and share lessons learned to maintain momentum and sustain the improvement process.
By proactively addressing these challenges and implementing appropriate strategies, organizations can harness the full potential of the PDCA cycle, driving sustained improvement and achieving operational excellence.
Create a plan for continuous improvement, with Dropbox as your base
A solid PDCA cycle needs secure, reliable foundations. Dropbox makes it easy to develop a clear Plan in one shareable, collaborative document, stored safely in cloud storage and accessible to your team, from anywhere.
Armed with your centralized project doc, you can easily share ideas or data files, ask for feedback, and start Doing. Collaborators can then analyze the data together thanks to real-time editing —recording results as the plan and actions are iterated upon.
Before you know it, you’ll have a clear, accessible record of the whole process, ready to Act on or refer back to for future PDCA cycles.
Don't miss out on the opportunity to transform your business and drive exceptional results with Dropbox as your base. Start a PDCA doc today and unlock the full potential of your organization.